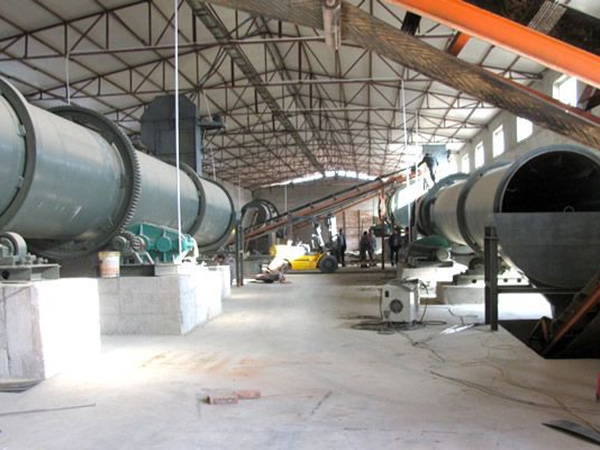
第一步污泥脫水發(fā)酵: 污泥從河道抽出脫水(脫水后的污泥水分含量在50% -60%)加入發(fā)酵劑進(jìn)行耗氧發(fā)酵,以殺死污泥中的病原體,寄生蟲卵和雜草種子,使污泥去臭達(dá)到無害化衛(wèi)生標(biāo)準(zhǔn)。
第二步粉碎: 把發(fā)酵好的污泥,運(yùn)行到半濕物料粉碎機(jī)內(nèi)進(jìn)行粉碎。
第三步拌料: 把粉碎后的污泥輸送到攪拌機(jī)內(nèi),使其原料水分充分均勻(水分含量在35%-38%)之間,為下一步造粒打好基礎(chǔ)。有條件的話可加入秸稈粉和微量的氮、磷、鉀,使其有更高的利潤(rùn)。
第四步造粒: 辦好的原料進(jìn)入新型造粒機(jī),新型有機(jī)肥造粒機(jī)利用高速回轉(zhuǎn)的機(jī)械攪拌力,使細(xì)粉狀料在機(jī)內(nèi)連續(xù)實(shí)現(xiàn)混合,成粒、球化、致密等過程,從而達(dá)到造粒的目的。顆粒形狀為球形,球形度≥0.7,粒徑一般在2-5毫米之間,成粒率≥90%,顆粒直徑的大小可通過物料混合量和主軸轉(zhuǎn)速適當(dāng)調(diào)節(jié),通?;旌狭吭降停D(zhuǎn)速越高,顆粒越小,反之亦然。
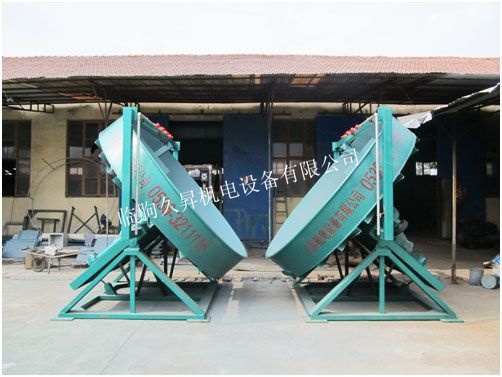
第五步烘干: 造好的顆粒從造粒機(jī)出來直接進(jìn)入烘干機(jī)烘干,烘干機(jī)可將高達(dá)50%-60%含水量的濕物料直接烘干至13%的國標(biāo)安全貯藏水分,整個(gè)過程在封閉系統(tǒng)內(nèi)進(jìn)行,從而減少干燥過程中對(duì)環(huán)境的污染。設(shè)備主要由熱源裝置、引風(fēng)機(jī)、和配電柜構(gòu)成;脫水后的濕物料加入干燥機(jī)后,在滾筒內(nèi)均布的抄板器翻動(dòng)下,物料在干燥機(jī)內(nèi)均勻分散與熱空氣充分接觸,加快了干燥傳熱﹑傳質(zhì)。在干燥過程中,物料在帶有傾斜度的抄板和熱氣質(zhì)的作用下,至干燥機(jī)另一段星形卸料閥排出成品。
烘干機(jī)特點(diǎn):
1.轉(zhuǎn)筒干燥機(jī)械化程度高,生產(chǎn)能力較大,可連續(xù)運(yùn)轉(zhuǎn)。
2.結(jié)構(gòu)優(yōu)良﹑簡(jiǎn)單﹑物料通過筒體阻力運(yùn)行平穩(wěn)﹑操作方便。
3.故障少﹑維護(hù)費(fèi)用低﹑功耗低。
4.適用范圍廣﹑產(chǎn)品干燥的均勻性好。
5.干燥的同時(shí)還可達(dá)到殺菌和除臭的目的。
第六步冷卻: 由于顆粒在烘干機(jī)內(nèi)流出后,自身溫度過高,直接裝袋容易起濕結(jié)塊。只有通過冷卻來解決。
第七步篩分: 冷卻后顆粒進(jìn)入篩分機(jī)篩分,確保顆粒大小均勻,不規(guī)則顆粒返回在生產(chǎn)。
第八步包裝: 自動(dòng)計(jì)量包裝機(jī)采用弧型門兩次給料方式,稱量方法簡(jiǎn)單 ,計(jì)量準(zhǔn)確穩(wěn)定,可用塑料袋包裝 ,使用高穩(wěn)定、高精度稱重傳感器、稱重模塊;界面操作簡(jiǎn)單、顯示直觀選用國內(nèi)外高品質(zhì)電器元件,確保設(shè)備可靠耐用 ,配備RS232和RS485接口,方便拓展 ,該秤結(jié)構(gòu)堅(jiān)固,占地面積小,易于清理和維護(hù) ,可選配主動(dòng)式回氣除塵裝置,吸凈浮塵,有效維持現(xiàn)場(chǎng)環(huán)境清潔。